Dive Deep: Insights About Aluminum Casting Processes
Dive Deep: Insights About Aluminum Casting Processes
Blog Article
Opening the Prospective of Light Weight Aluminum Spreading: Proven Methods for Success
Aluminum spreading has long been acknowledged for its versatility and prevalent applications across various industries - about aluminum casting. Discovering the full possibility of this procedure calls for more than simply standard understanding. By applying proven approaches honed through years of sector experience and innovation, producers can raise their light weight aluminum casting procedures to new elevations of efficiency and high quality. From optimizing layout factors to consider to simplifying manufacturing procedures, the vital lies in using these methods properly. Join us as we explore the necessary elements that can move light weight aluminum spreading towards unequaled success in today's open market landscape.
Advantages of Aluminum Spreading
Light weight aluminum spreading provides a plethora of advantages that make it a recommended selection in various commercial applications. Among the main advantages of light weight aluminum casting is its light-weight nature, which adds to sustain efficiency in industries such as vehicle and aerospace. Furthermore, light weight aluminum is extremely flexible, permitting complicated and detailed forms to be conveniently generated through casting procedures. This adaptability in style is a significant advantage for markets that call for parts with specific geometries.
Furthermore, light weight aluminum casting gives superb rust resistance, making it optimal for applications where exposure to extreme atmospheres is an issue. The product also shows excellent thermal conductivity, which is valuable for markets needing warm dissipation, such as electronic devices (about aluminum casting). Moreover, light weight aluminum is completely recyclable, straightening with the growing focus on sustainable practices in modern production.
Design Factors To Consider for Casting
When considering casting layout, meticulous focus to detail is vital to ensure the effective production of top notch parts. The layout phase plays an essential duty in the general success of a light weight aluminum casting job. One crucial consideration is the choice of suitable geometries and attributes that promote the casting process. Developers should take into account factors such as draft angles, fillets, and wall density to ensure appropriate metal circulation and solidification throughout spreading.
Additionally, considerations related to parting lines, gating systems, and risers are important to protect against problems like porosity and contraction. It is vital to optimize the layout for efficient material use and minimize post-processing needs. Simulations and prototyping can be important devices in assessing and improving the spreading design before major production.
Partnership between layout suppliers, engineers, and factories is vital to address any kind of prospective obstacles early in the style phase. By including these factors to consider into the spreading design procedure, makers can improve product quality, decrease expenses, and eventually open the full capacity of light weight aluminum casting.
Enhancing Casting Performance
When aiming to enhance casting performance in light weight aluminum spreading tasks,Creating with a focus on enhancing material flow and decreasing problems is vital. To accomplish this, utilizing simulation software application can help in identifying prospective concerns before the spreading procedure starts. By simulating the flow of liquified aluminum, developers can change gating and riser styles to ensure appropriate filling and solidification, ultimately reducing the incident of flaws such as porosity or shrinkage.
In addition, applying proper heat treatment processes can improve the total spreading performance. Warmth therapy can help improve the mechanical properties of the aluminum spreading, ensuring that the final part satisfies the required requirements. In addition, utilizing automation and robotics in the spreading process can enhance manufacturing, decrease find out here hand-operated labor, and boost overall efficiency.
In addition, continuous monitoring and quality assurance throughout the casting procedure are critical for identifying any kind of discrepancies and making sure that the final products meet the preferred requirements. By carrying out these techniques, manufacturers can enhance casting effectiveness, boost product high quality, and ultimately achieve higher success in light weight aluminum casting jobs.
Quality Assurance in Light Weight Aluminum Spreading
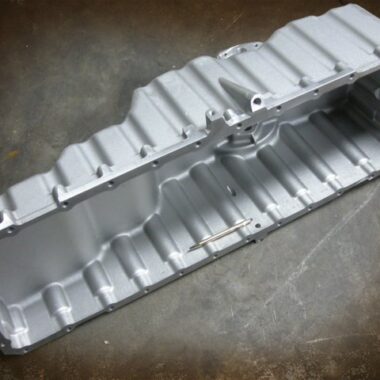
Efficient quality assurance practices play a crucial duty in making certain the accuracy and dependability of aluminum spreading procedures. Quality assurance procedures in aluminum casting encompass a variety of tasks focused on maintaining specific standards and recognizing inconsistencies that could compromise the end product. These techniques begin with the careful choice and evaluation of basic materials to assure their high quality and suitability for the casting process. Surveillance and controlling the criteria of the spreading procedure itself, such as cooling, temperature level, and stress rates, are critical action in preserving uniformity and stability in the final products.
In enhancement to process control, top quality control in aluminum casting includes rigorous screening and inspection treatments at different stages of production. Non-destructive screening methods like ultrasonic screening and X-ray evaluation aid spot inner flaws without endangering the stability of the cast elements. Visual examinations, dimensional measurements, and mechanical testing even more make certain that the actors components satisfy the required requirements and efficiency requirements. By applying robust top quality control practices, aluminum casting facilities can provide products that satisfy customer expectations for reliability, top quality, and performance. he has a good point
Making Best Use Of Productivity
To achieve ideal economic efficiency, a thorough approach for making best use of earnings within aluminum spreading procedures should be carefully developed and implemented. One vital element of making the most of earnings in aluminum spreading is optimizing production effectiveness.

Moreover, expanding item offerings and exploring new markets can assist increase profits streams. Recognizing customer demands and market trends can direct calculated choices to utilize on emerging possibilities. Spending in research and growth to introduce processes or products can likewise drive productivity via differentiation and client complete satisfaction.
Final Thought
To conclude, aluminum spreading uses countless benefits in regards to design versatility, cost-effectiveness, and sturdiness. By meticulously taking into consideration layout considerations, boosting casting efficiency, executing high quality control measures, and maximizing productivity, manufacturers can open the full possibility of aluminum casting. This versatile and dependable process has confirmed to be an effective selection for a large range of commercial applications.
Additionally, aluminum is highly flexible, permitting for intricate and intricate shapes to be quickly created why not look here through casting procedures.Reliable high quality control practices play an essential role in making sure the accuracy and dependability of aluminum casting processes.In enhancement to procedure control, high quality control in aluminum spreading entails rigorous screening and assessment procedures at numerous phases of manufacturing. By implementing durable quality control techniques, light weight aluminum spreading facilities can provide products that fulfill client expectations for high quality, reliability, and efficiency.
By very carefully taking into consideration layout considerations, enhancing casting performance, carrying out high quality control steps, and making best use of earnings, manufacturers can unlock the complete potential of light weight aluminum casting.
Report this page